Remember when we had to push an actual button in order to trigger our devices to perform an action?
Thanks to capacitive touch technologies, sensors are now replacing buttons and membrane switches across a broad range of consumer electronic devices, from smartphones and tablets to laptops and other similar electronic devices. At Cardinal Peak, we recently completed a capacitive touch project that overcame some interesting demands. In this post, we’ll review how the technology works and how we adapted it to an unusual environment.
Contents
How Do Capacitive Touch Screens Work?
Using an electrostatic field and measuring the minute changes to the capacitive field, capacitance-based touch sensors transform a surface area into a multitude of sensing opportunities. Such sensors can detect and measure anything that is conductive or has a dielectric different from air, enabling non-mechanical methods of receiving that stimulus.
Capacitive sensing (or cap sense) relies on the transfer of energy within an electrical network or between distant networks by means of a displacement current between circuit nodes, induced by the electric field. Or more simply “capacitive coupling.” One “circuit node” is a conductive media driven by the cap sense circuit, attached to an overlay surface. The overlay must be nonmetallic in order to sense effectively. The other circuit node is anything conductive or has a dielectric other than air, such as a finger.
What Makes Capacitive Touch Sensing Possible?
When it comes to your finger, human body tissues are filled with conductive electrolytes covered by a layer of skin, creating the conductive property that makes capacitive touch sensing possible. Thus, in order to work on capacitive touchscreens primarily designed for fingers, styluses, gloves and other instruments have to simulate the difference in dielectric offered by a finger.
How Do Capacitive Proximity Sensors Work?
Capacitive “proximity” sensors take this further by sensing even smaller changes to the electrostatic field at greater distances. In the end, capacitive sensors provide developers a lot of flexibility in terms of what they can do with their user interface because they’re not tied to a mechanical membrane switch or a button.
Capacitive Sensing Applications
While touch sensors have been around for years, recent advances make capacitive-based sensors a practical alternative to buttons and mechanical switches in a wide range of consumer products. Since the launch of the first iPhone, touch sensing technology has revolutionized how we interact with machines of all types across environments.
Leveraging capacitive sense technology, computer trackpads, digital audio players, smartphones and tablets use touchscreens as input devices. Such screens typically consist of a capacitive touch sensor, at least two complementary semiconductor integrated circuit (IC) chips, and application-specific IC controller and a digital signal processor (DSP).
Driven by technological advances, capacitive sensing functionality has become quite prolific within microcontrollers, and in many cases, the technology has become off the shelf for a lot of microcontrollers on the market. This ultimately frees engineers from worrying about the timing, circuitry, and all of the algorithms and innards of the signal processing. Out-of-the-box technology can detect the actual capacitive change, measured in incredibly small units called femtofarads (fF).
Today, capacitive sensors enable users to control products. They convert surfaces, flat or curved, into keyboards, turn the volume up or down — whatever the user interface happens to be. From proximity, pressure, position and displacement to force, humidity, fluid level and acceleration, myriad sensors use capacitive sensing to prompt action.
Unlocking Capacitive Sensing Tips and Tricks
At Cardinal Peak, we recently completed a consumer electronics smart home project for one such input device using capacitive sense technology — a battery-powered smart door lock.
Going into the project, we knew we wanted to leverage proximity sensing so that the lock would operate at a lower quiescent power and sense a user’s keycard as it approaches the lock. The aim of this approach was primarily to conserve the battery. This way, the circuit could turn on the reader, read the card, then turn the reader off to save power and extend the battery life.
The challenge: The lock is constructed of a metal (conductive) housing. The lock could be attached to a wide range, type and style of door, including a metal door, that could be either electrically isolated or conductive to the lock housing.
This presents a significant design challenge and the simple development board, cookie-cutter approach is no good. Because the electrostatic “sense field” wants to capacitively couple to anything conductive (the return path), and the changes to the capacitive field are very small (femtofarads), any surrounding conductive surface can and does act as a return path, bleeding off energy from the electrostatic field. This “parasitic capacitance” reduces or eliminates the sensitivity, defeating the design intent and ensuring the lock design would not satisfy requirements.
A capacitive touch sense area is a conductive area, like a gas tank, that holds a specific limited amount of energy. Any parasitic capacitance acts like a human digit or specialized input device, diverting that energy and decreasing the capacitive field, which thus decreases the sensitivity. So, stay away from metal! But seriously, in some cases, sacrifices can be made to our benefit. A ground can be put around the actual sensor in order to wall it off or isolate it from noise. But again, it bleeds off your sensitivity, which may be fine — or possibly desired — for “touch” but rarely when “proximity” sensing.
The better approach is to implement shielding of the sense element, by way of a guard ring, trace or shield. Guards or shields are placed around and/or under the sense area in order to buffer or block charge-stealing parasites. Not all capacitive touch microcontrollers or application-specific chips have this capability, so choose wisely.
With this approach, the shield driver is an active signal output that is driven at the same voltage potential of the sensor input(s), so there is no potential difference between the shield and sensor input. Energy is taken from the shield and not the sense elements. As is often the case, the smart lock combines the digital logic and keypad with the cap sense. We also want a nice ground plane on our printed circuit board (PCB) and follow best design practices. Cap sense can seem to be directly opposed to doing what is right. With a shield, we are not only able to direct the sensing zone to a particular area, we also reduce parasitic capacitance caused by the housing and mitigate other interfering capacitance and noise.
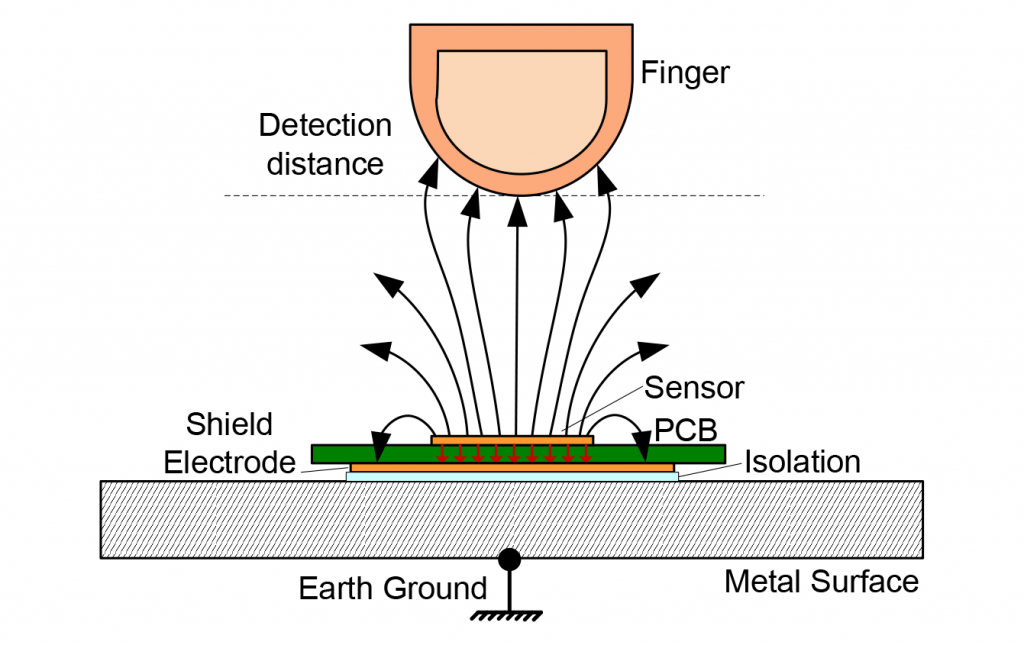
A shield electrode decreases the metal case’s influence on the sensor’s electrical field propagation. (Source: Cypress Semiconductor)
Capacitive Sensing: Art and Science
As we discover with every project, capacitive sensing can occasionally be more of an art than a science. Application notes and papers do a pretty good job and have the information to get your design most of the way. The biggest challenge lies in not forgetting about the physical location of how everything fits together. The art is being able to give your sense area a pathway and be able to route that without any interference.
The “design guy’s” recommended choice is to use a chip with multiple output channels or, better yet, specific guard or shield outputs. In developing the lock, we took a failed attempt, improved the layout of the actual board itself, implemented any and all shielding, knowing the lock body was going to be a significant issue. Through these techniques, and by finding a chip with multiple output channels and guard pins, we were victorious and were able to turn off the high-power circuit and use a lower-power proximity circuit to detect the close presence of a user’s card. While the metal housing challenge never went away because it’s a physical property of the lock and the environment, we were able to increase the sensitivity of the proximity sense area. To an extent, we reduced the drive level of the proximity sensor, reducing power consumption even further.
Clearly, capacitive sensing is not as simple as just finding a chip, slapping it down and expecting it to work as designed. And copying of an evaluation board layout is ill advised. There’s an art to it. At Cardinal Peak, we know what we’re doing. We’ve learned a significant amount from previous projects like the smart lock, and we know how to effectively implement the technology.
Today, touch sensors are cost-effective to implement in a wide range of consumer products, and they also enable higher sensitivity and reliability of sensing circuits to increase overlay thickness and durability. To discover how we can use capacitive sense and other innovative technologies to help bring your next consumer device project to life, give us a shout!